Getting to Net Zero: Part III
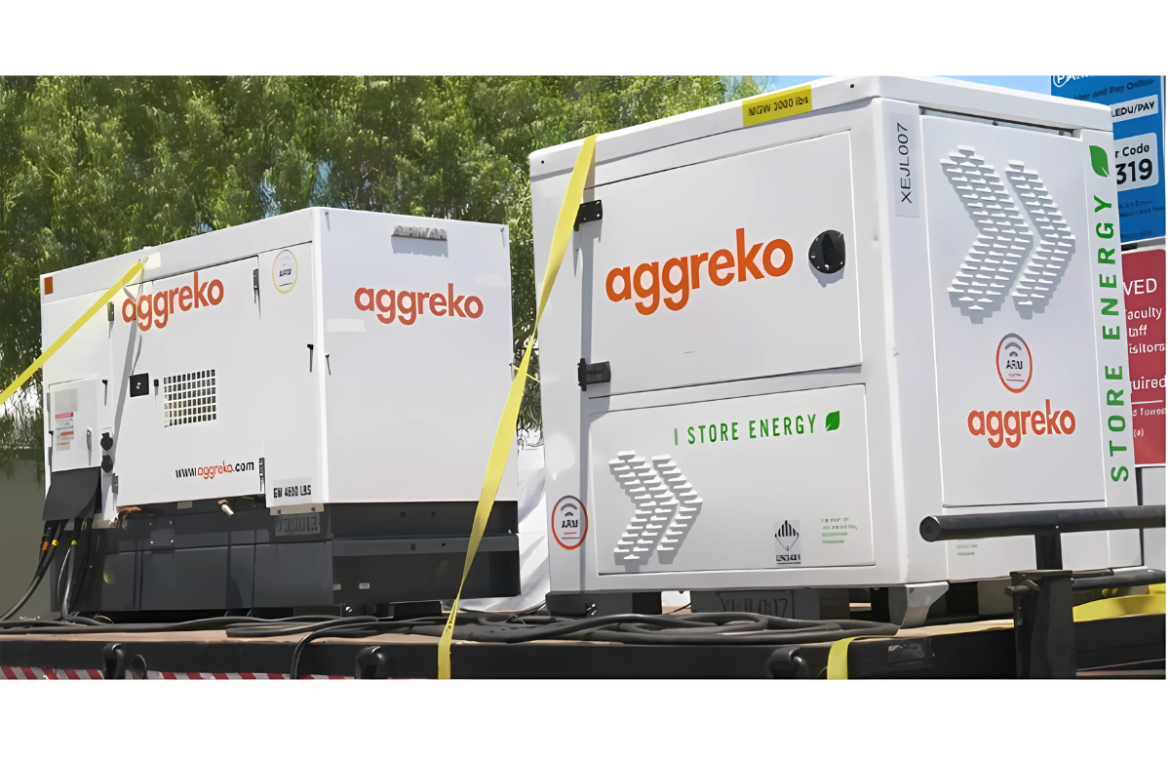
The introduction of mobile Battery Energy Storage Systems (BESS) has led to a paradigm shift in how power is sourced, distributed, and managed on movie sets and in live events. For example, in part one of this series (18 Sep 2024), we discovered that it is possible to get to net-zero production with mobile BESSs that can be paralleled to increase capacity and runtime. In part two of this series (17 Mar 2025), we discovered that the “hard” power of BESSs eliminates the need to isolate non-linear loads on separate power sources – greatly reducing the number of generators required. In this part we will look at how BESSs have changed how we size power sources for loads.
A power source is either “hard” or “soft” depending on the degree of voltage waveform distortion created by the current drawn by non-liner loads. We say the power from diesel generators is “soft” because it is susceptible to load induced distortion of the voltage it generates. The power from the grid is “hard” because it is not. The degree to which a power source is susceptible to distortion of its voltage waveform determines the quality of its power, or “power quality”, and how reliably equipment will operate on it.
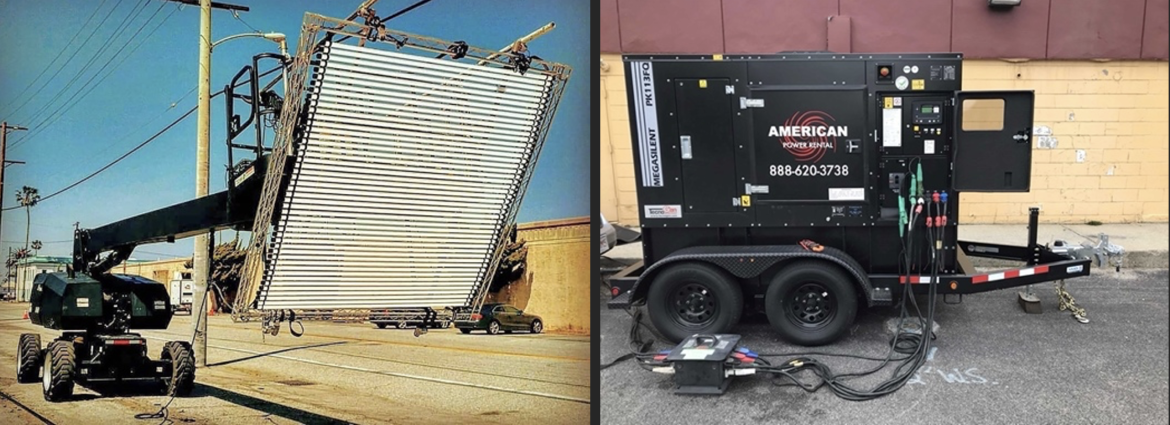
Figure 1: Left, a large soft box consisting of Quasar Science LED tubes. Right, the additional generator we used to power it on the Ryan Reynolds Apple series Defending Jacob
Many of the issues we experience with diesel generators are the result of the current harmonics drawn by non-linear loads encountering the impedance of the generator that can be as much as 20x higher than the grid. The resulting voltage waveform distortion (Figure 3) can have deleterious effects on connected loads not seen on hard power sources.
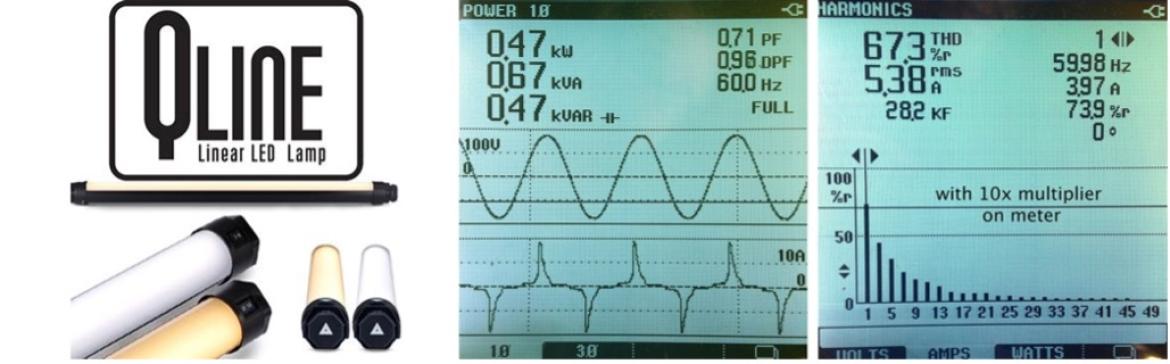
Figure 2: PQM readings of the Quasar Science LED tubes on grid power. (Note: disproportionate amount of third order harmonics (third, ninth, etc.) in the FFT on the right).
BESSs generate hard power. Which means we must no longer oversize our power source by a factor of two, the way we do with diesel generators, in order to avoid voltage waveform distortion, like that in Figure 3, when powering predominantly non-linear loads like non-pfc HMIs, Kinos, and LEDs.
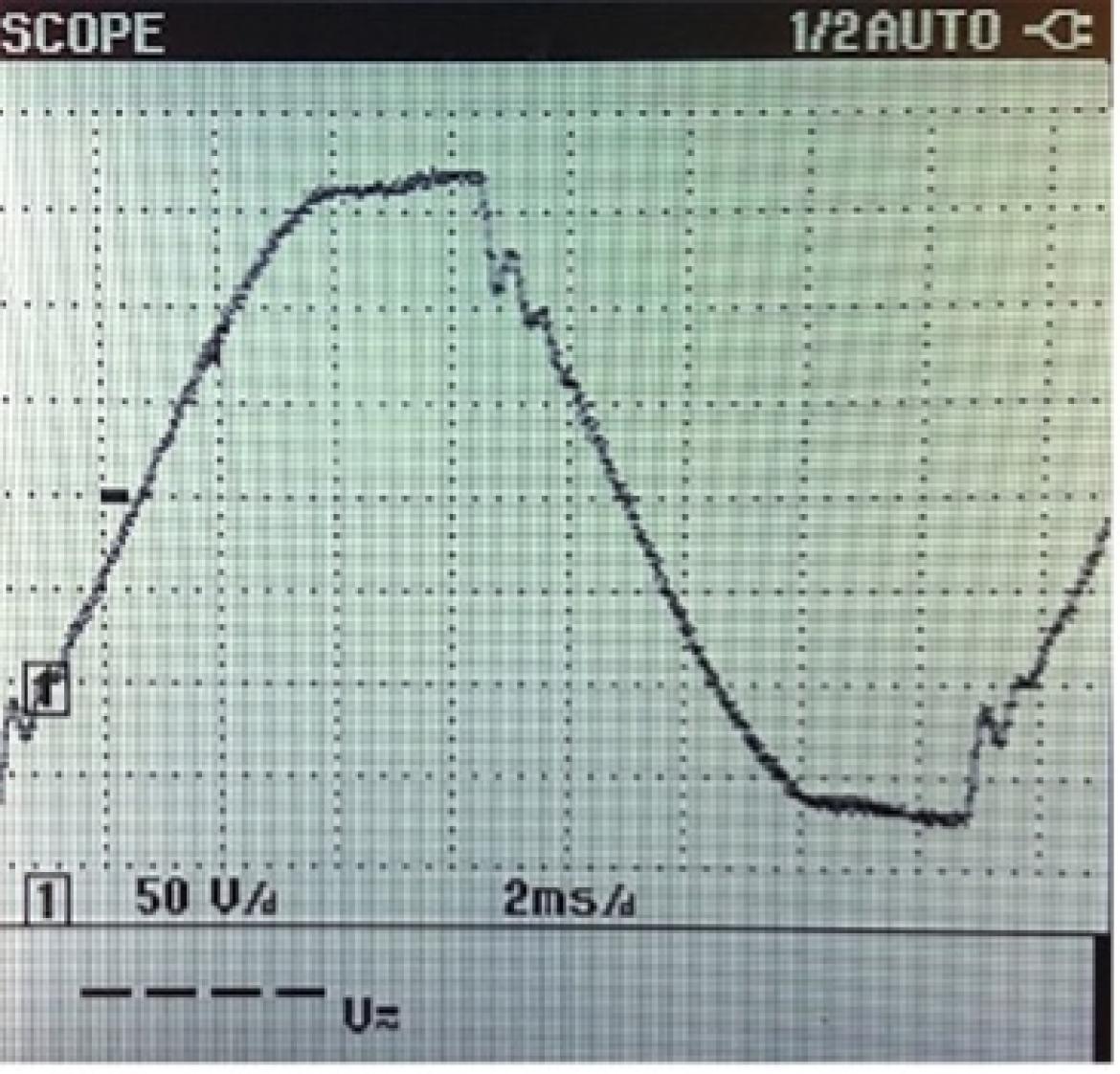
Figure 3: PQM reading of the voltage waveform distortion caused by LEDs operating on the soft power of a generator.
Such high voltage distortion can be problematic for other loads connected to the same power, especially those that utilize Switch Mode Power Supplies (HMIs, Kinos, LEDs) because they only draw current at the peak of the AC waveform when the voltage is higher than the voltage of the energy stored in their smoothing capacitor/s. Appreciably flat-topped voltage that doesn’t reach the normal peak value of 169.7 V (120V RMS x a Crest Factor of 1.414) has the effect of reducing the energy stored in the capacitor/s. With less stored energy, a Switch Mode Power Supply’s capability to ride through such distortion of the voltage is reduced and power to the ballast’s switch mode converter can be interrupted causing the light to flicker or shut down as illustrated in Figure 4.
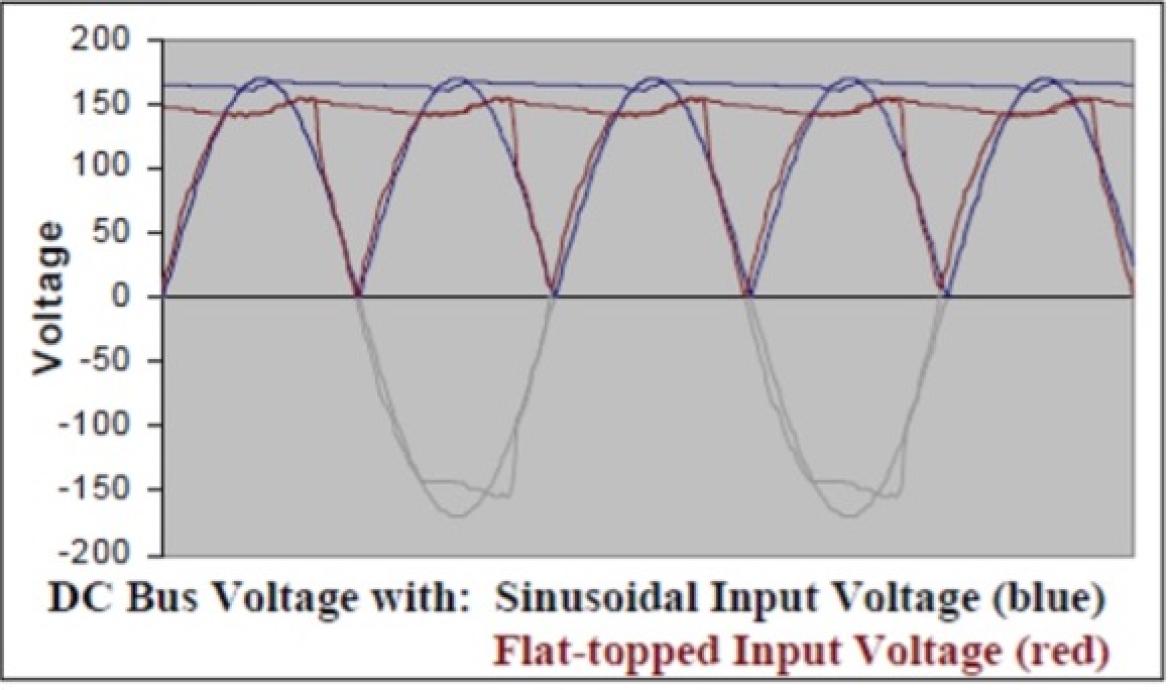
Figure 4: Why high voltage distortion can be problematic for connected loads that utilize SMPS. (Illustration courtesy of Mirus International)
While there is no firm limit to voltage harmonic distortion in the US, IEEE 519 recommends that non-linear loads utilizing SMPSs operate on power with no more than 5% THDV. Otherwise, their DC bus voltage will be reduced from what the equipment is designed for, starving it of power, causing it to flicker or shut down. This goes for not only LED fixtures, but also HMI and Kino fixtures, as well as audio and video recording equipment that use SMPSs to convert AC mains power to DC. That the harmonics drawn by non-linear loads does not cause voltage waveform distortion of the hard power of BESSs, means they can be right-sized for the load rather than over-sized.
Another paradigm shift in how we size a power source for a load comes when the load is not evenly distributed. For example, a common use application for both diesel generators and BESSs in motion picture production is the powering of two 18kW HMI lights on a maned equipment work platform, or MEWP for short (Figure 5 below).
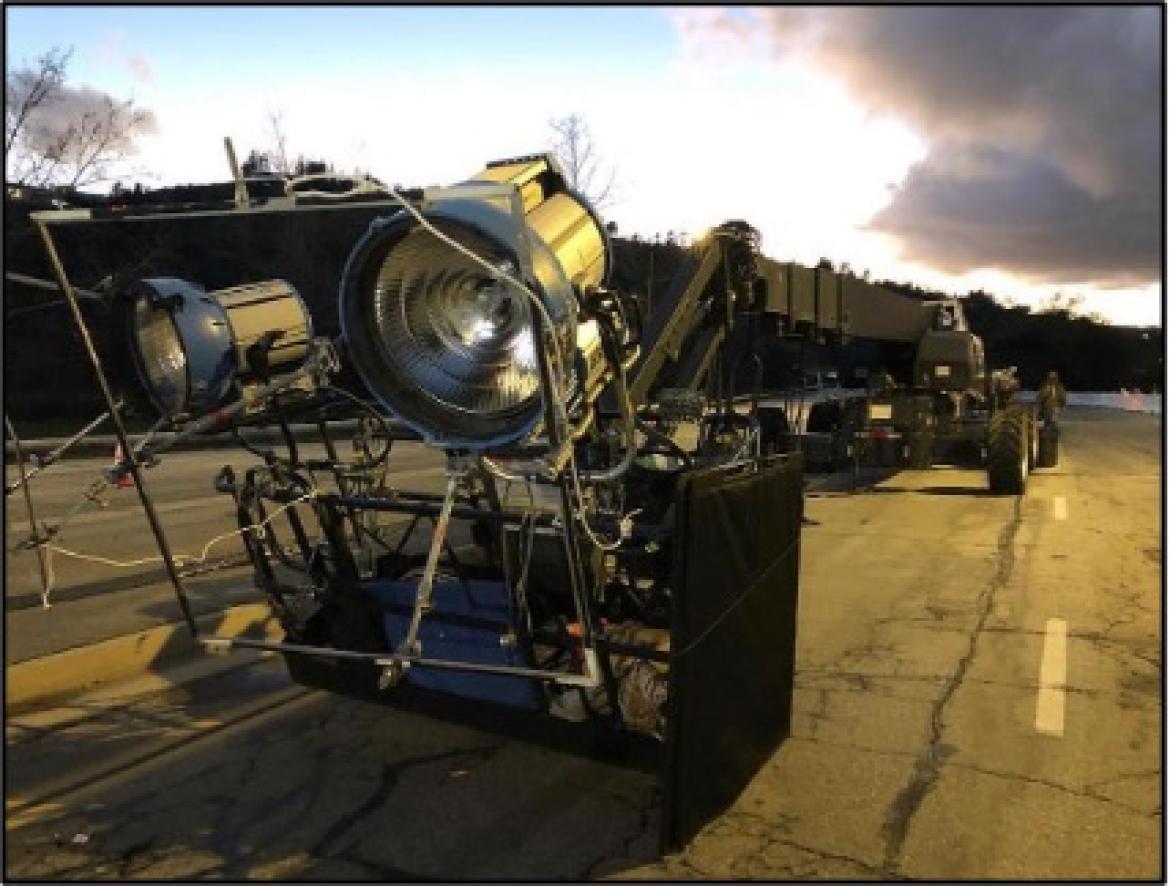
Figure 5: Two 18kW ARRIMAX HMI fixtures in the basket of a MEWP.
At 208V, an 18kW HMI draws about 80A/phase on two phases of a 3-phase distro. Operating two on 3-phase power would draw 80A on two legs and 160A on the third (see distribution table in Figure 6 below.) When sizing a diesel generator for this application, we must use at least a 70kW plant to accommodate the high leg of 160A.
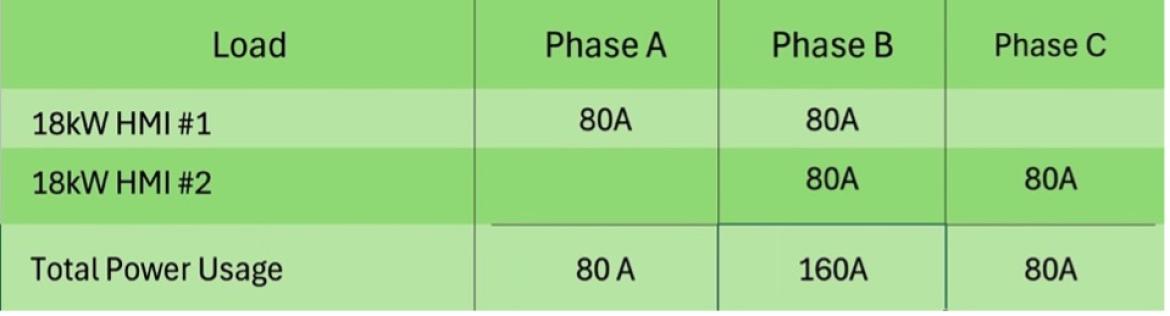
Figure 6: distribution of load generated by two 18kW ARRIMAX HMI fixtures on a 3-phase distro. Note: high leg of 160A.
As a rotating machine, large imbalances between the phases of a diesel generator (100% in this case) results in significant heating in its windings, voltage regulation difficulties, and waveform distortion due to magnetic asymmetries. Sizing rules for diesel plants take this into account by using the maximum current on any leg to calculate the size of the plant required. Because diesel generators have poor tolerance for current imbalance, the current on the high leg becomes the determining factor when sizing them for a load. Which means that, even though the overall load in this case is only 36kW (2 x 18kW HMIs), a 70kW generator capable of supplying 160A per phase must be used to accommodate the high leg (kW = (VL x I x 1.732 x pf) ÷ 1000 = (208V x 160A x 1.732 x .98) ÷ 1000 = 56.5kW x 1.25 for a continuous load = 70.6kW). Given that, one would think that at least a 70kW BESS would be required, but that is surprisingly not the case because of an inherent difference in how diesel generators and BESSs operate.
Phase current symmetry is not required to maintain waveform integrity or internal operational balance in BESSs because their power control system (PCS) generates power for each phase independent of the others while drawing from a common DC bus. When phase loads are unbalanced, the PCS compensates for the imbalance by generating more current for the high leg independent of the current it generates for the low legs. Since energy is drawn from a common DC buss, the load is balanced internally on the DC side, not the AC side. In other words, the power demand on each phase is met independently by the PCS generating the required current from the common DC energy source, and the DC bus absorbs the net energy imbalance, while the PCS constantly monitors AC output to ensure stability. The result is that large phase-to-phase current discrepancies at the AC output do not result in destabilization of the power source as it does with diesel generators, provided the total real and reactive power draw remains within system limits.
That’s not to say that set electrics should not strive to balance loads in 3-phase distribution systems when using BESSs. We balance phases not only because large imbalances result in significant operational issues with diesel generators, but for other reasons as well. For example, when the impedance of the system neutral is high, unbalanced phase currents also generate unbalanced phase voltage sufficient to shut down 18kW HMIs regardless of whether the source is a diesel generator or BESS. Tightly balancing the load on the distribution system reduces the disparity in phase voltages for both power sources when the impedance of the system neutral is high.
In this case (powering two 18kW HMIs), the only constraint on the size BESS is whether the output connectors and protective elements (breakers, contactors, current sensors) of the BESS are capable of sustaining 160A on a single phase continuously without excessive voltage drop or thermal stress. Since the BESSs we use are primarily designed to operate with diesel generators in a hybrid configuration where the BESS passes thru, and assists, the power from the diesel plant (some BESS can add up to 125A/phase to the power passing through from a generator), their connectors and protective elements (breakers, contactors, current sensors) are typically over-sized for their rated output. For example, the PowR 2 XPro 60 (Figure 8) can pass through 200A/phase in hybrid operation with another AC source. To that, it can add up to 55A/phase, for a total output of 250A/phase (the size of its breaker), which means the current rating of the XPro 60 (250A/phase) is more than sufficient to accommodate the high leg of 160A when powering two 18kW HMIs on a 3-phase service.
But that’s not all: The use of BESSs in conjunction with diesel generators, enables the use of smaller diesel generators operating more efficiently. If the object is to reduce CO2 emissions, the use of a diesel generator may seem counterproductive. It is not. If designed and used properly, a hybrid energy system (HES), consisting of a diesel generator and BESS working in tandem, can be a valuable tool in the transition away from fossil fuel-based production. In its current state, this technology is not suitable for set lighting applications because set lighting is a continuous load but is a natural fit for charging BESSs in movie basecamps or whenever there are peak and off-peak demand periods.
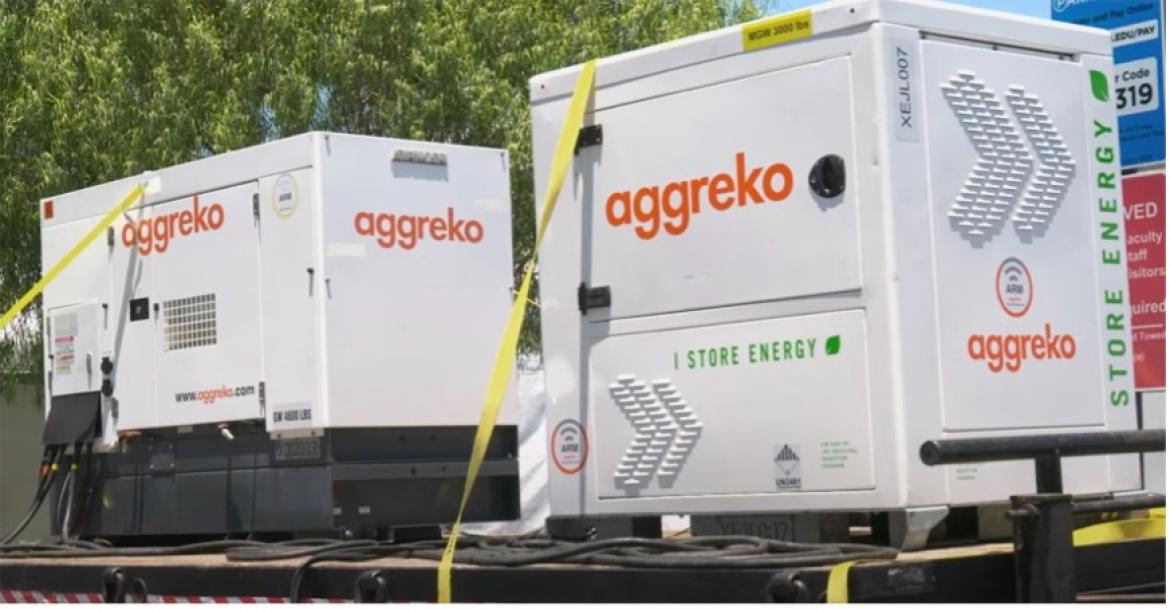
Figure 7: A hybrid set up consisting of 70kVA diesel generator (left) and 60kW/120kWh PowR 2 XPro 60 (right).
A HES consisting of a diesel generator and a BESS reduces CO2 emissions by several means: Diesel generators operate most efficiently above 70% of their prime rating. As can be seen in the graph below (Figure 9), operating the generator at reduced loads of less than 30% can be inefficient and result in higher fuel consumption and CO2 emissions per kW of energy produced.
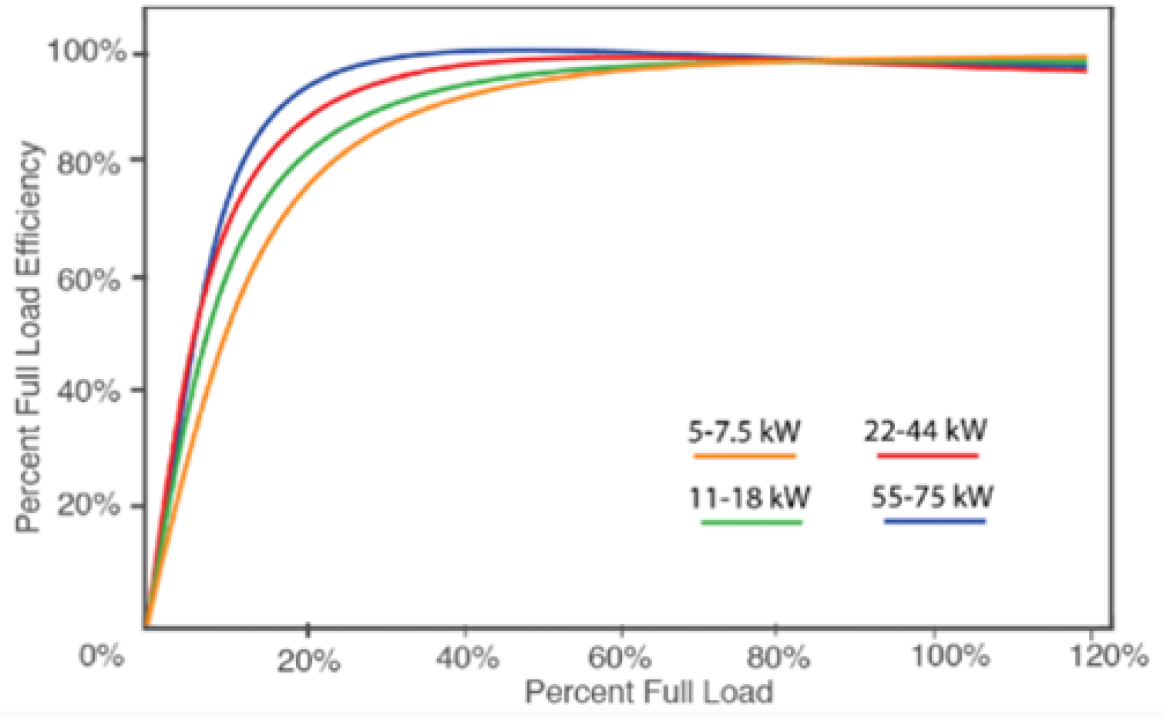
Figure 8: During periods of low demand (< 30% of its prime rating) a generator operates inefficiently, leading to unnecessary CO2 emissions.
A HES can reduce or eliminate inefficient operation of generators by using stored energy in the BESS to power off-peak loads when the generator would otherwise be running inefficiently. When the batteries are almost depleted, the generator can be brought online to power loads while simultaneously charging depleted batteries. When the batteries are full, the generator is switched off and the batteries again provide power to off-peak loads. When in this seamless cycle the generator is running, it will run more efficiently, with less CO2 emissions, with the added load of charging batteries.
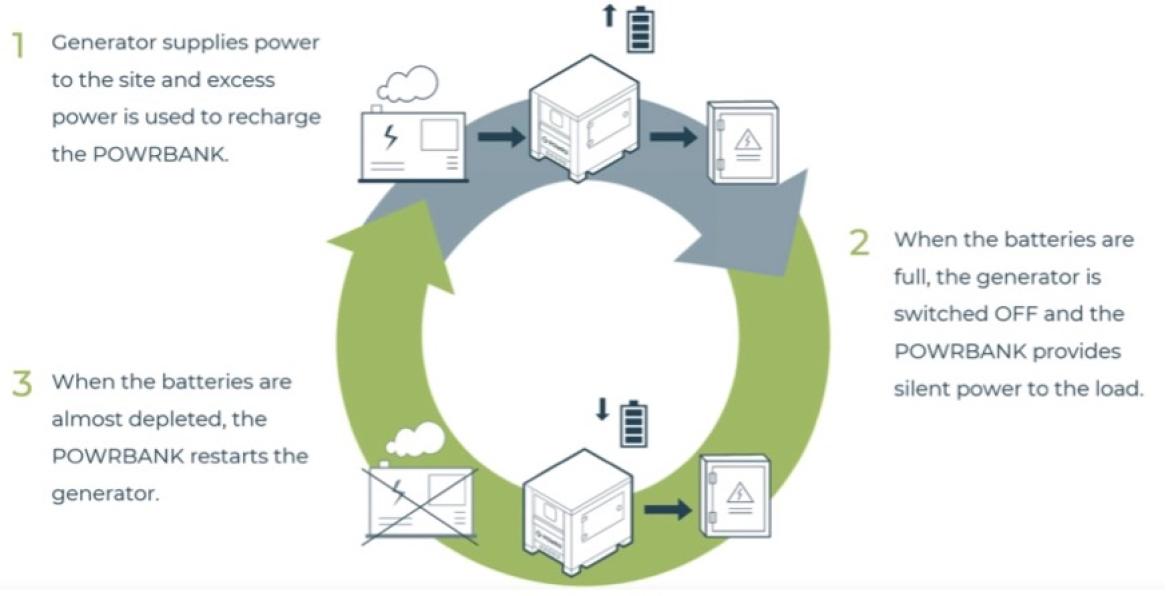
Figure 9: The seamless dis-charge/charge cycle of HES (Illustration courtesy of PowR 2)
The key to this approach, called load sharing, is under-sizing the generator. Smaller generators that emit less CO2 can be used since the BESSs of most manufacturers can “assist” a generator. For example, if peak load is 200A/phase, a 60kVA generator with an output of 166A/phase can be used and the deficit of 34A/phase supplied by a BESS, like the PowR 2 XPro 60. In other words, the BESS will ‘top-up’ the input power supply if the load demands more power than the generator can deliver. This is possible because many BESSs, like the PowR 2 XPro 60, have the unique ability to conform the phase angle and voltage waveform of the power they generate to that passing through from a generator.
To operate efficiently and emit less CO2 emissions, the generator must first be sized so that the combined load (peak demand plus what it takes to charge batteries) is equal to 80% of the generator’s prime rating when it operates most efficiently and generates the least amount of CO2 emissions. The generator should then be under-sized by the amount of power the BESS can contribute to assist the generator in meeting this combined load. That way, during peak demand periods, the BESS can share the load by supplying additional power, thereby reducing the size of the generator required – further reducing the amount of CO2 emissions generated.
Any situation that has periods of peak demand and off-peak demand can benefit from this approach. What makes load sharing ideal for powering movie basecamps while charging batteries for other applications, is that on a macro level, basecamps have peak and off-peak periods. The period of peak demand depends on the time of year and/or what part of the country the production takes place. For example, in the Northeast United States during the heating months (Sept-May), the load profile of a mid-size basecamp consisting of the big three (HMU, Wardrobe, and Honey Wagon trailers), plus eight Star-Trailers, will draw upwards of 200A/phase first thing in the morning as the heaters of all the trailers come online at once to warm them up. Once warm, the load of the trailers drops, but is still high from crew prep activity. Between HMU blow dryers, Wardrobe steamers, and Star-Trailer activity, basecamp loads can be as high 150A/phase until everyone moves to set, at which point basecamp loads drop to about 50A/phase, or less, for the remainder and better part of the production day.
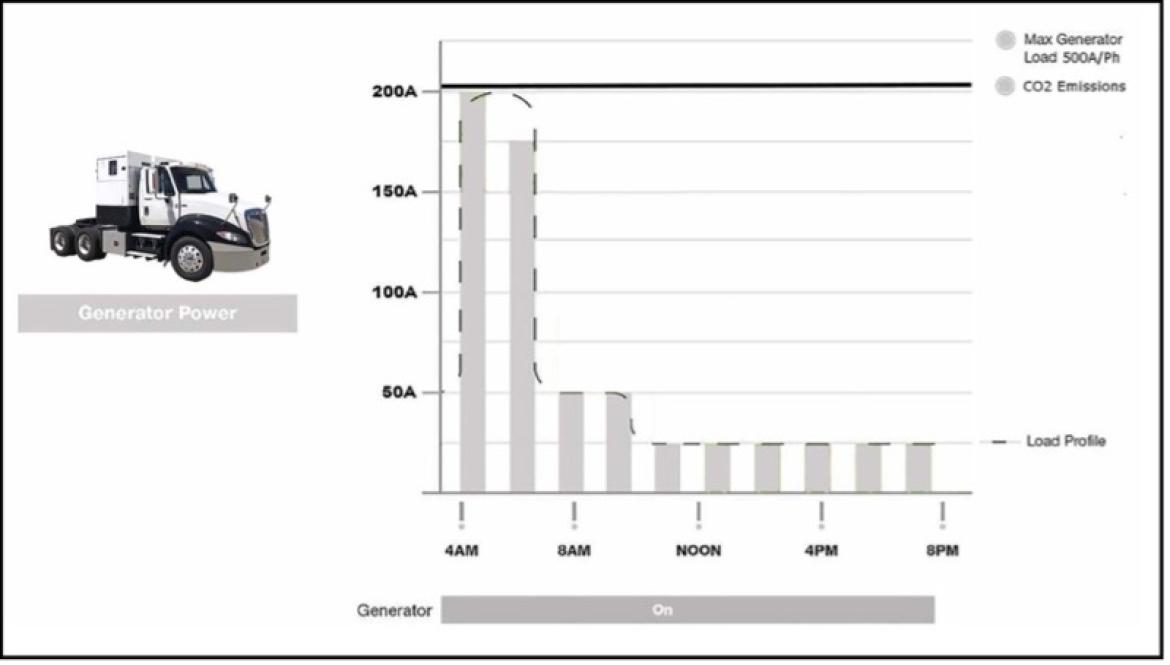
Figure 10: As illustrated the 1400A tractor mounted diesel generator that typically powers basecamps are underloaded 100% of the time.
Which means that, as illustrated above in Figure 11, the 1400A tractor mounted diesel generator that typically powers basecamps are underloaded 100% of the time, and severely underloaded 85% of the time, which results in excessive CO2 emissions.
Given this characteristic of basecamp, we can cut CO2 emissions by using the excess capacity of the generator to charge, not only batteries to power basecamp during off-peak periods, but also charge batteries for other applications as well – such as construction, catering, VFX, and set lighting. With the additional load of charging multiple BESSs, the total load on the generator is higher so it burns fuel more efficiently and generates less CO2 emissions.
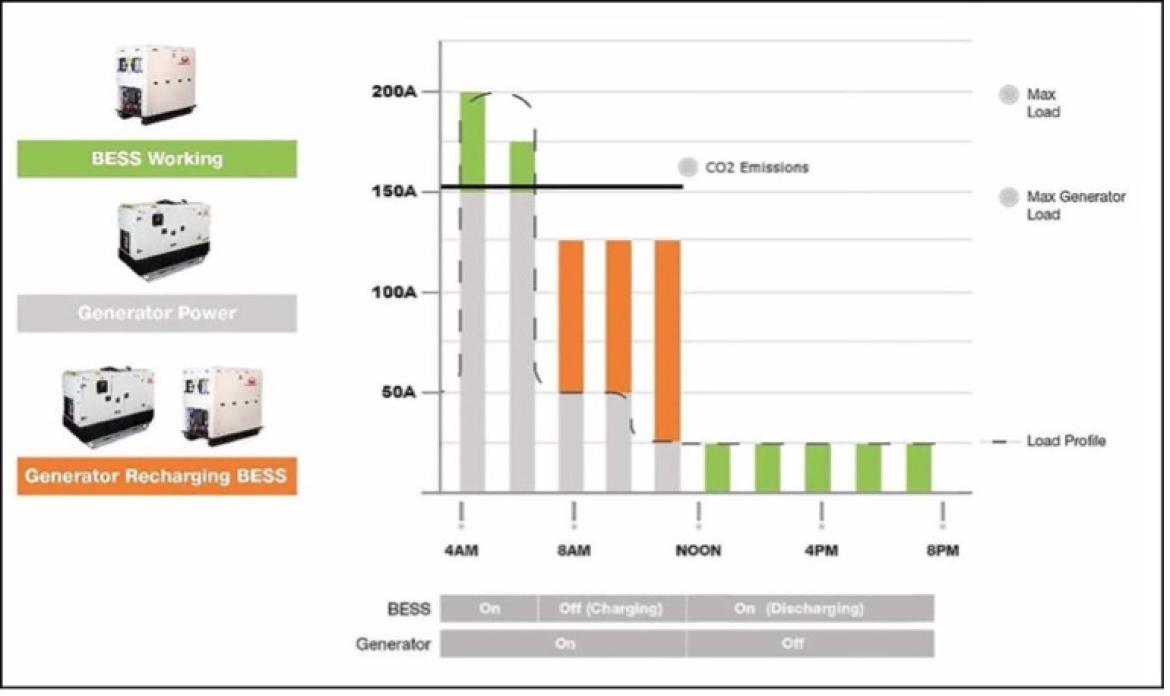
Figure 11: To meet peak demand in the morning, a BESS can assist a diesel generator. As demand drops, the excess capacity of the generator can be used to charge the BESS while simultaneously powering the basecamp. During off-peak periods, the generator is shut off and the BESS powers the off-peak load of basecamp.
When basecamp loads drop after crew moves to set, and the charging of BESSs is complete, the generator can be turned off and the off-peak load of basecamp can be carried for the remainder of the day by the BESS designated to power basecamp, while the rest are deployed to power set lighting and the many side-shows of a movie production. If for some reason, the BESS powering basecamp should run down before the end of the day, the generator can be brought back online.
Things get a bit more complicated during the cooling season (June-Sept) when the peak demand is during the middle of the day to cool the trailers. But if we look at a concrete example, we see that a HES is still a good fit. For example, the Jon Hamm comedy, Confess Fletch, was shot during July/August in the Boston area. That basecamp drew upwards of 100A/phase during peak demand at noon to cool the trailers and was about 20A/phase off peak in the mornings and in the evenings when the trailer AC units were idle. In this case, a BESS would provide 100% of the power in the morning and evenings, while the generator provides power during the peak load in the middle of the day. To assure the most efficient operation of the generator in this case, additional BESSs for set lighting and other applications would be recharged in the middle of the day.
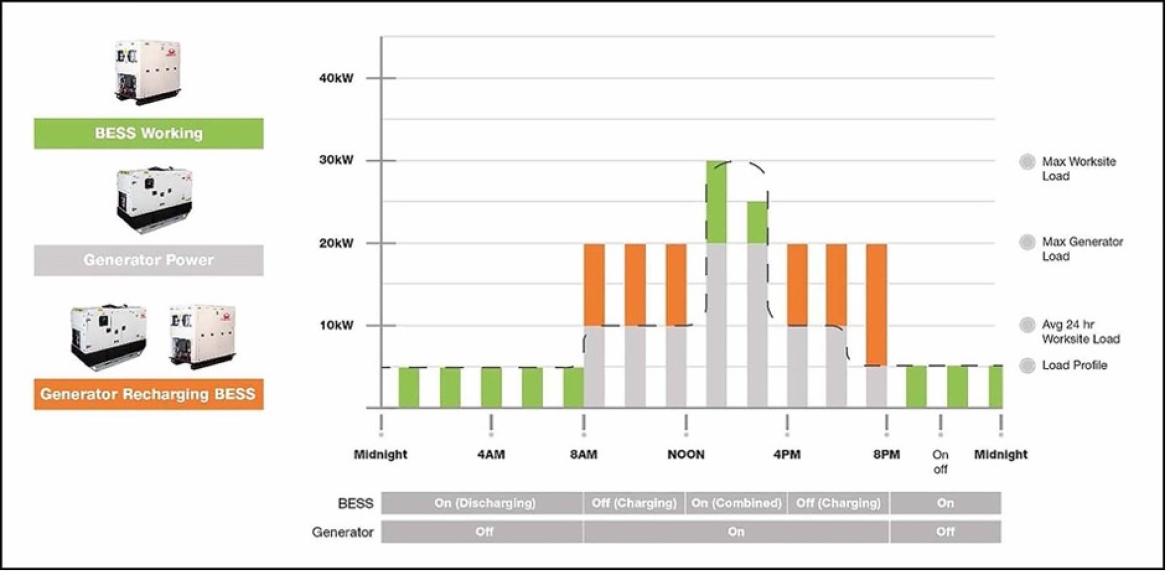
Figure 12: during the cooling season when the peak demand is during the middle of the day to cool the trailers, the BESS assists the diesel generator. During the shoulder times, the generator charges the BESS. During off-peak periods, the BESS carries the load.
By implementing these strategies, an under-sized generator/BESS hybrid system can not only reduce the CO2 generated to power basecamp, but also the entire show, since the generator is used to charge BESSs for not only its basecamp load but set lighting and the many side-shows of a movie production as well.